Too many people today assume new insights must come from advanced IIoT monitoring systems or AI platforms, but actionable insights do not require high-tech tools. Simply learning something new about your assets or how to care for them (as opposed to operating based on assumptions or incomplete knowledge) can lead to big improvements in reliability, decreases in costs or both.
John Clancy is a Maintenance Inspector
at the Argos Cement Plant in Newberry, Florida.
John Clancy, Maintenance Inspector at the Argos Cement Plant in Newberry, Florida, understands the power of knowing - and how quickly that knowledge can spread. He is part of the Methods Department, the plant’s reliability group, and has been working with Noria to improve lubrication at the plant.
“In the Methods Department, which was started in 2015, there were originally five of us: two inspectors, two planners and one coordinator,” John said. “We have now moved up to three inspectors, three different planners, a coordinator, two first-level inspectors and two lube techs.”
This process did not happen overnight, but the journey to better lubrication at the Newberry plant began when a former supervisor took John and another inspector to a conference where they met a Noria expert and got his business card.
“When we came back, our company was wanting us to move forward with our lubrication program,” John said. “We remembered meeting Noria and liking what they had, so we dug up the business card and reached out. From there, it just flows right into meeting Devin.”
Devin Jarrett, Customer Success Manager at Noria, has helped many plants improve lubrication, but Argos was different from most other plants.
“Argos has dedicated inspectors - that is what their jobs are,” Jarrett said. "There aren’t a lot of plants out there that have people who are dedicated to just inspection tasks.”
This emphasis on inspections is just one of the ways that the Argos plant did things a bit differently from most organizations. It is part of what has helped the plant implement lubrication improvements so effectively. The other aspect was its corporate team’s involvement in the process.
Corporate Support
The first thing that Noria does for clients looking to improve lubrication is assess their program. While many lubrication assessments are focused on simply consolidating lubricants (usually to fit a certain lubricant supplier’s offerings), Noria's Ascend™ Assessment is comprehensive, holistic and aligned with international standards (learn more at noria.com/ascend).
John remembers the moment when he heard the Newberry plant’s Ascend Assessment score - it wasn’t what he or others in the Methods Department expected.
“Devin asked us, ‘Where do you feel your lubrication program is right now?’ And he took all of our opinions on it,” John said. “I think we said some 70s, some 80s and things like that.”
The Ascend Assessment is scored out of 100, but what may surprise some is the average score across industries. It turned out that the Argos Newberry plant was right in line with this average score.
“Devin came back and said, ‘No, you’re more like a 30 right now,’” John said, laughing. While this was not what the Argos Newberry team had hoped to hear - it did represent a significant opportunity that the corporate team recognized.
“The methods department team at the Newberry plant were very open and receptive to the knowledge we provided them during the Ascend Assessment,” Devin said. “Even their corporate team in South America was involved in the process, so they got to hear firsthand what we were doing with John and his team.”
Having the corporate team involved in the process sends a strong message to everyone at the plant that lubrication is an important part of the larger reliability program. John said that the involvement of the corporate team was essential to getting the job done. “Without their support or influence, we couldn’t have achieved any of this,” he said.
Quick Wins
Some of the first improvements that were put in place were related to grease and regreasing practices. In the past, the Argos team had set grease intervals on electric motors to once per year. In examining their assets, it became clear that some motors needed more frequent regreasing, at least twice per year. Another quick fix was switching from guessing the right amount of grease to knowing the right amount. Grease storage was also an area of opportunity.
While the Newberry plant had a designated storage area for oil lubricants, grease was stored in a variety of locations - including the trunks of electricians’ service trucks. The hot Florida sun was impacting the performance of the grease, so one of the first improvement recommendations was to designate a grease storage area with less harsh conditions. This would help avoid large temperature changes or exposure to environmental contaminants that impact the performance of stored greases. The Ascend Assessment identifies “low-hanging fruit” like this, along with many more opportunities.
The next step is to complete the Engineering Design phase of the process. During this phase, Noria experts gather engineering data from all lubricated assets and make hardware recommendations to improve inspections, lubrication practices, contamination control and many other aspects of lubrication.
When the issue of grease storage was identified, the Newberry plant was able to address these concerns quickly by designating a grease storage area within an existing space in the plant. Improvements like this can offer excellent returns on investment because they do not always require significant added expenses.
“There are things that we can do that don’t cost any money,” Devin said. “They just come down to having a different mindset or mentality and doing the work a certain way.”
The updated grease room was a very visible sign of change, one that had a ripple effect through the plant. Other departments saw the clean, shiny new area that the lubrication team had created and asked themselves what they could do to improve other areas of the plant in the same way.
Argos stored some greases in this area,
but without the right mindset or plan,
greases were unorganized
and not properly controlled.
With the grease room updated with
proper storage equipment and
procedures, greases are no longer cooked
in the Florida sun before use.
“Just by us doing the lube room cleanup or modifications, I think that alone changed a lot of people’s mindsets on what they were doing,” John said. “There were even a couple of emails that went out saying ‘look what the lube team has done with their equipment and their lube room,’ and it sparked other teams to modify or improve other areas of the plant.”
Improved Procedures
Another quick win was spreading knowledge of improved regreasing procedures. While the plant has two lube techs on staff who are trained to handle most lubrication tasks, the plant’s electric motors are regreased by electricians. Since these electricians are responsible for overall maintenance of the motors, they needed proper equipment and knowledge to do the job right.
New grease guns with counters allow electricians
and others to put just the right amount of
grease when it is needed — no more guesswork.
The Newberry plant supplied these electricians with new grease guns equipped with counters (or “output meters”). Combined with engineering calculations and OEM recommendations, the electricians now had the knowledge and tools to properly regrease their motors, allowing lube techs to focus on more complex lubrication tasks.
The value of these improvements is multiplied when they are spread to more people in the plant in this way, but John said that certain hardware modifications had an even bigger effect on lubrication culture.
Visible Lubrication Culture
A major part of Noria’s Engineering Design recommendations is outfitting machines with hardware to improve inspections, better protect machines and help extend lubricant life by excluding or removing contaminants. Once the recommendations have been made, the third phase of the process is Implementation. Finding the right hardware for the job that aligns with best practices is not always easy, but each piece of hardware can be vitally important for the long-term success of a lubrication program.
For John and his team, the upgrade from a dipstick to a columnar level gauge on many machines was a major improvement.
“I would say that the best thing we’ve seen from the hardware is having sight glasses vs. a dipstick,” he said. “I think ‘columnar level gauge’ is the technical name for them, but it gives anybody that walks past it a visual of what oil is in whatever piece of machinery. And it’s got little green and red rubber bands on it.”
Those little green and red rubber bands might seem small, but they have had a big impact on lubrication culture in the plant because they are a clear visual indicator, even to the untrained eye.
“It makes it easier for the person who doesn’t know what they’re looking for,” John said. “If you take anybody from the front office or who doesn’t deal with lubrication at all, and they walk past a gearbox that has a dipstick, they aren’t going to think about it. But if it has this big sight glass on it with clear red and green lines - and everyone knows green is good and red is bad - he can understand it without really even knowing what he’s looking at.”
In this way, the hardware helps not only lube techs and inspectors to quickly and easily check on their machines; it also turns anyone in the plant into an inspector. If you can see oil is below the red line, you can report a low oil level just by glancing at the machine.
Visible hardware changes can have such a big impact on lubrication culture. They are constant reminders of the importance of lubrication, and they give quick and clear insight into the health of machines. This is why John believes that this simple gauge has had such an impact on how lubrication is seen in the plant.
“Is it technically the most important change?” John said. “Maybe not - maybe the sample ports are really the single most important piece of hardware in the program. But I would say that the best thing we’ve seen from the hardware is having sight glasses versus a dipstick.”
A columnar level gauge provides a simple visual indicator
that anyone can understand with its green and red bands.
The connected desiccant breather helps
protect the reservoir from contaminants as well.
Knowing Your Oil
While the columnar level gauge may have contributed more to lubrication understanding and culture change in the plant, John said the improved sampling procedures provided by Noria, along with new oil sample ports, have truly been the most important change in terms of lubrication insights.
“The sample port is going to give you the fluid of your equipment, whatever it may be,” he said. “Your fluid is the lifeblood of the equipment - it’s what keeps it alive and working. You can take samples all day long, but if you’re not taking them correctly, you’re not getting useful information.”
Because samples can become contaminated so easily if proper hardware and procedures are not in place, many plants do not realize how much their oil analysis is impacted by improper sampling. This is something John has seen firsthand.
“Your sample is only as good as how you took it,” he said. “The sample ports minimize contamination and cross-contamination and make your sample that much more truthful.”
Getting to the real truth of your oil can be an eye-opening experience. When you truly know your oil and what it contains,, you can take action to improve cleanliness over time, extending the service life of your oil and of your machines.
Buddy, a Lube Tech, takes a sample using
a new sample port while following improved procedures.
Long-Term Goals
In addition to these short-term successes, the Argos Newberry plant is already looking ahead to long-term goals. The corporate team is a major part of this effort. They have seen the improvements at the Newberry plant and are already considering how to get more value from these changes by spreading that knowledge to other Argos plants.
“They have mentioned that once we get our plant here fully going 100% with these changes, they’re probably going to send me to one of their other plants to implement it at those facilities,” John said. “To me, for them to say that they’re interested in implementing it in another plant shows that they’re interested in the long-term.”
In this way, the Newberry plant can serve as a “pilot program” for improving lubrication at other sites. Any successes there can be more easily replicated by knowledge transfer from skilled and driven leaders like John.
Advice for Others Leading Lubrication Change
John Clancy has accomplished a lot in his time working with the Noria team, but it did not happen by accident. From the beginning, Devin said that John took lubrication seriously.
“I’ll never forget at the end of their Ascend Assessment delivery, with everyone in the room, John looked at me and very pointedly said, ‘Thank you for doing this.’ My eyes have been opened. And it is going to be my job to take this on and fix it, and I will fix it,” Devin said. “From everything that I’ve seen, he’s very much lived up to those statements that he made in front of his team at Newberry.”
John is not the type to publicize his achievements - he’s just interested in getting the job done right, but we asked him what he would tell others who are considering stepping up to improve lubrication in their plant today.
“The only advice I would give to someone who is stepping up for something like this is: Be open, because you don’t know everything,” he said. “You have to be open and willing to move forward with what you’ve learned.”
And John, along with the whole Newberry team, has done just that - their openness to new information and their problem-solving abilities have carried them through the process, even in the middle of a pandemic. Their commitment has allowed them to improve reliability through better lubrication, drive sustainable lubrication culture change and cut down on unnecessary costs at the same time.
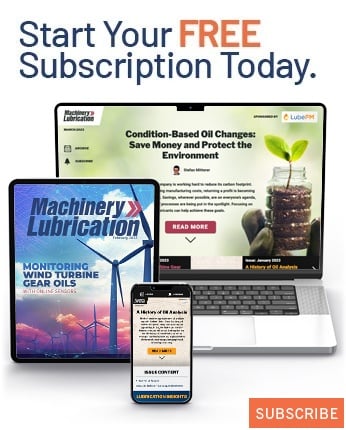